MAN ES’s ammonia-fuelled two-stroke engine clears another hurdle
Length: • 7 mins
Annotated by Marc Chasserot
Marc Chasserot: Take some highlights and try this prompt again. MAN Energy Solutions has successfully tested a two-stroke engine running on ammonia, which is a zero-carbon fuel. The Danish engine designer plans to launch a full-scale, slow-speed engine capable of running on ammonia by the end of this year or early 2024, with the aim of having such an engine ready for commercial operation in a ship by 2026. Safety is a major concern with ammonia, as it is toxic to humans, but MAN ES has taken precautions to address these concerns. Shipowners have shown openness to green ammonia as a future alternative fuel, feeling its environmental and commercial benefits are compelling.
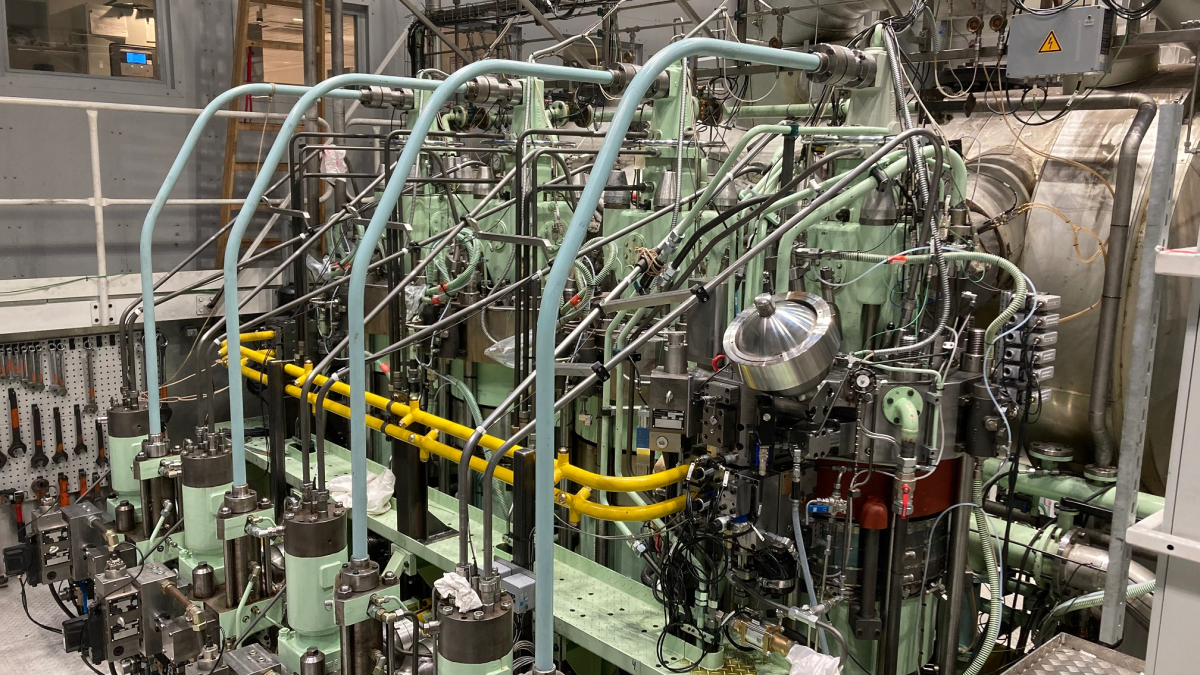
The Danish engine designer reports the successful completion of combustion testing of a two-stroke engine running on ammonia, keeping its timeline intact for full-scale engine introduction by year’s end, or early 2024
Much of maritime’s decarbonisation journey hinges on research and development being conducted in Europe and Asia by two-stroke marine engine designers. There, researchers are trying to do something that has not been done before — build a powerful ship engine capable of burning ammonia, a zero-carbon fuel, to help fulfil shipping’s net-zero emissions ambitions by 2050.
One of those engine designers is MAN Energy Solutions (MAN ES). Already successful in developing a portfolio of two-stroke, dual-fuel, high-pressure marine engines capable of combusting LNG, methanol, and LPG, based on its ME-GI engine platform, MAN ES has set its sights on unveiling a full-scale, slow-speed engine capable of running on ammonia by the end of this year, or in early 2024. Clearing this hurdle enables MAN ES to hold steady to its timeline of having such an engine ready for commercial operation in a ship by 2026.
The Danish engine designer reported completing another milestone in July, with the successful testing of the first two-stroke engine running on ammonia at its Research Centre Copenhagen (RCC). Combustion tests were performed on an MAN B&W two-stroke 4T50ME-X type and produced positive results, with particularly promising data regarding pilot-oil amount and combustion stability, reports MAN ES.
“This successful combustion represents yet another, important step”
Commenting its testing, MAN ES CTO, Gunnar Stiesch, said it was part of ongoing research to gain “a deep understanding of ammonia’s unique characteristics as a marine fuel, as well as its effects on fuel supply and safety systems. This successful combustion represents yet another, important step towards decarbonising the marine market and bringing big things to zero.”
Safety is a primary concern with ammonia, as it is toxic to humans. Limited exposure, either as a vapour or liquid, could be deadly.
This is why MAN ES has taken a number of precautions in testing its ammonia-fuelled engine technology, including the construction of a custom-built ‘cold hall’, which can contain ammonia vapour in the event of a leak with the activation of a water screen. Robust safety features from the company’s existing dual-fuel portfolio, such as double-walled piping and system ventilation, have also been built into the ammonia engine’s design.
Because of these safety concerns, not everyone believes ammonia is the right path for shipping at this juncture. One of those is energy major Shell. In its All-Hands-on-Deck 2.0, Industry Perspectives report released in June, Shell writes: “Safety concerns persist regarding toxicity mitigation and with limited development of propulsion technology. Until advances are made that can address these concerns, Shell does not believe ammonia will be a viable bunkering fuel for shipping.”
But shipowners have shown their openness to considering green ammonia as a future alternative fuel, feeling its environmental and commercial benefits (particularly in light of forthcoming carbon taxes) are compelling, as it contains no carbon. Additionally, they are also confident that the technical and safety issues are solvable through collaboration across the supply chain.
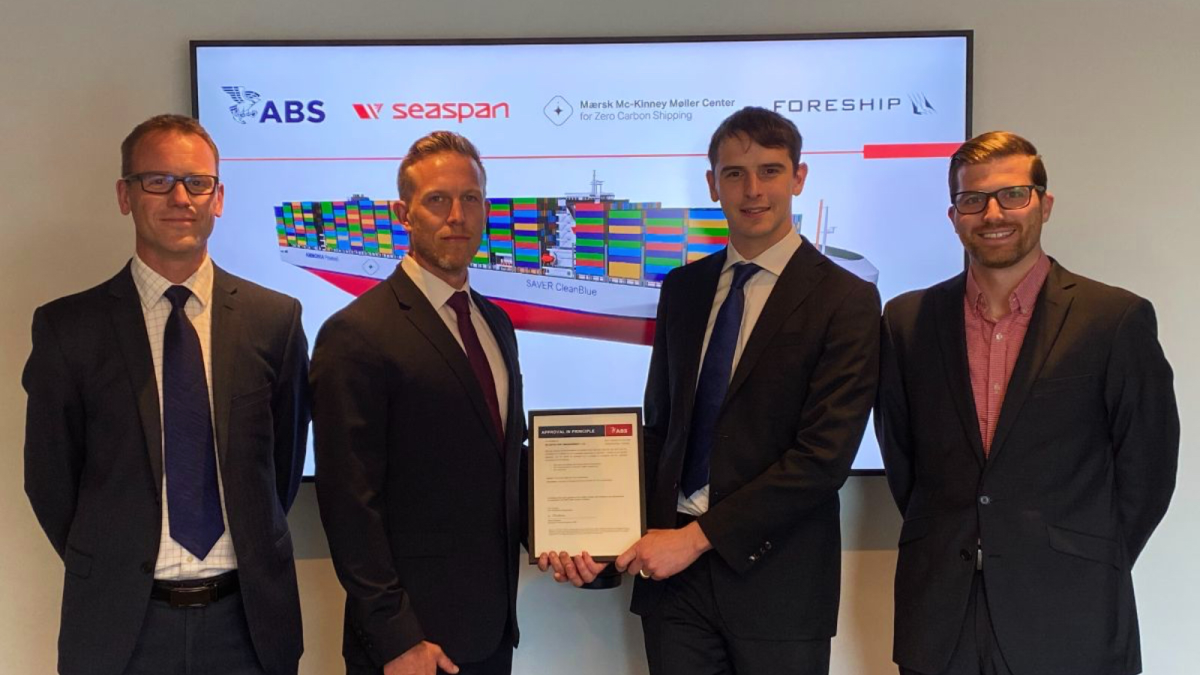
Ammonia-powered ULCS
Seaspan Corp, for example, pioneers in LNG-fuelled ships and, more recently, methanol conversions, received an approval-in-principle (AiP) from ABS for an ammonia-powered, 15,000-TEU ultra large container ship (ULCS) in July in Copenhagen. Seaspan was joined in the project by the Maersk Mc-Kinney Møller Center for Zero Carbon Shipping (MMMCZCS) and ship designer Foreship. The project included defining the safety objective, the impact of ammonia as a fuel on vessel performance, completion of a hazard identification (HAZID) qualitative risk assessment and development of the concept design.
Documentation included fuel range and endurance analysis, ammonia tank and system location assessments, general arrangement, main machinery and electrical system design and initial vessel stability calculations.
The project is connected to the Singapore Ammonia Bunkering Feasibility Study (SABRE) consortium, focusing on developing and demonstrating an ammonia supply chain in Singapore. Phase 1 performed an end-to-end technical and commercial feasibility study of ammonia bunkering in Singapore, along with a preliminary ammonia bunkering vessel design.
“Safety concerns persist regarding toxicity mitigation”
The project is now in Phase 2, investigating how to mature the commercial feasibility so that contractual terms across the supply chain are prepared and can be executed to establish an ammonia bunkering operation in Singapore. The 15,000-TEU ULCS was designed as a potential receiver of ammonia fuel from bunker vessels currently under design and development.
Seaspan Corp senior vice president, assets and technology, Peter Jackson, said the project was “a good example of industry collaboration, where leading maritime organisations are working together and taking tangible steps to decarbonise the maritime industry. Ammonia is a promising future marine fuel, and this project is a vital and significant step in the development and realisation of ammonia-powered container ships.”
Mærsk Mc-Kinney Møller Center for Zero Carbon Shipping head of ship design, Thomas McKenney, added: “This project highlights the importance of collaborative design development and proper safety-case integration as the ammonia fuel pathway matures for the maritime industry.”
ABS vice president, global sustainability, Panos Koutsourakis, said: “This landmark vessel is an important step towards helping shipowners and operators benefit from ammonia’s zero-carbon tank-to-wake emissions profile. However, ABS recognises that ammonia presents a specific set of safety and technology challenges, and we are committed to leading the industry in supporting its safe adoption at sea.”
More recently, ABS issued an AiP to Korean Maritime Consultants (KOMAC) for an ammonia-fuelled, 3,600-TEU container ship. KOMAC is forecasting there will be an increase in demand for these smaller-size ships fuelled by ammonia.

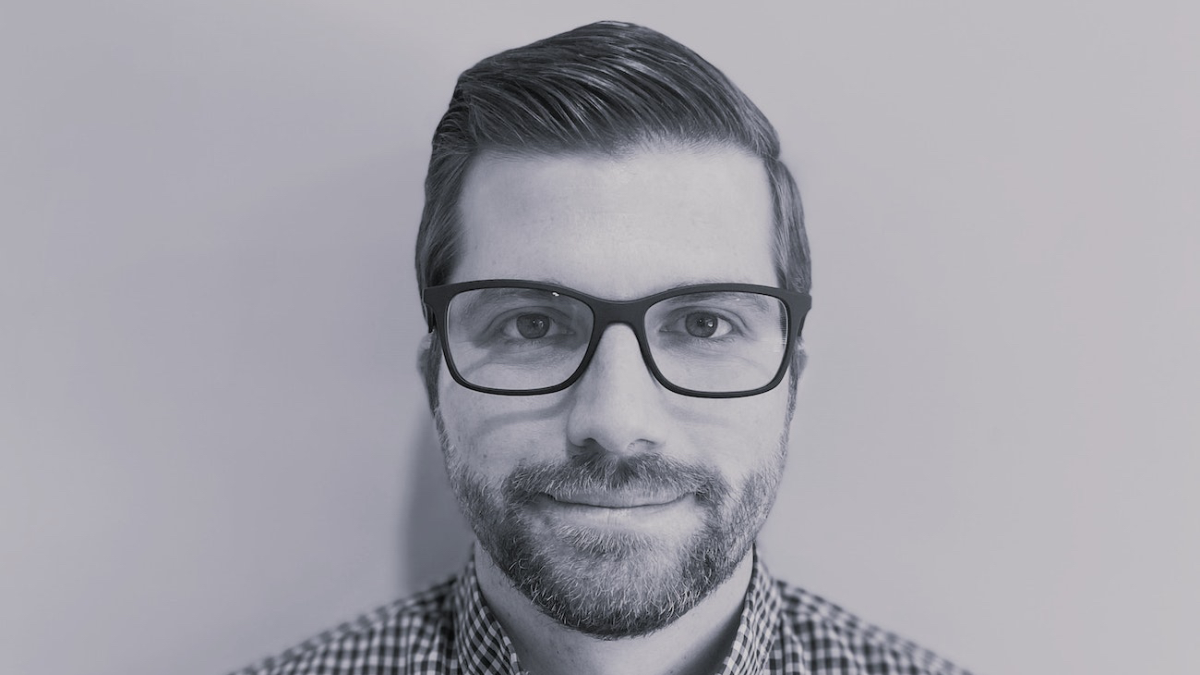
Ammonia-fuelled gas carrier concept
MMMCZCS plans to release a report detailing the concept design, how the ammonia safety case was developed and outcomes from the risk assessment. The potential commercialisation of the vessel design concept, based on technology and shipyard readiness, will be the focus of the next stage of this project.
In another project, the Nordic Green Ammonia Powered Ship (NoGAPS) MMMCZCS is collaborating with a number of stakeholders, including MAN ES, on developing an ammonia-powered gas carrier that can carry ammonia.
According to the design description, the gas carrier is being optimised for operation between the Gulf of Mexico and Northern Europe, with a speed of 15 knots and 12,000 nautical mile endurance. The gas carrier’s three bilobe Type C semi-refrigerated tanks will have a total capacity of 22,000 m3. The boil-off gas from the cargo is handled by reliquefaction units located in the cargo handling room on deck. The gas carrier has three semi-refrigerated Type C fuel tanks located on deck, with a total capacity of 2,700 m3. It will have fuel and reliquefaction handling rooms located in a deckhouse on the ship’s port side. The fuel handling room receives fuel from the storage tanks, where it is prepared to be sent to the main engine. Fuel supply leaves the fuel valve train at an increased pressure of 80 bar and passes through a double-wall pipe to the engineroom. To achieve optimal emissions, while reducing risk and cost, the main engine is the only ammonia consumer on board. Propulsion power will be supplied by a single two-stroke, 7.2-MW ammonia-fuelled main engine, equipped with a shaft generator. Ammonia emissions will be managed through the engine design and a selective catalytic converter.
“Ammonia presents a specific set of safety and technology challenges”
Ammonia combustion presents several challenges related to safety, climate and the environment. Among these is ammonia slip, which is unburned ammonia that escapes in the combustion process. This is highly toxic, presenting a safety risk for crew and passengers on board the vessel.
Another risk is NOx, formed by incomplete ammonia combustion, which presents a health risk to local communities where vessels operate and must be managed to maintain regulatory compliance.
N2O generated during the ammonia combustion process has a GWP 273 times more potent than CO2 on a 100-year timescale, according to the US Environmental Protection Agency.
Due to ammonia’s poor combustion characteristics, a secondary or pilot fuel will be required in the ignition process. If this pilot fuel is fossil based, it will result in CO2 emissions.
Japan Engine Corp (J-ENG), which plans to introduce its first ammonia-fuelled two-stroke engine in 2025, is applying its stratified injection technology with pilot fuel to address ammonia’s hard-to-ignite characteristics. Explains J-ENG: “Stratified injection with pilot fuel and post fuel (ammonia) in multiple layers can realise an utmost combustion control and optimise a high suppression of N2O emission, which is said to have a high global warming coefficient, through [an] improved mixed fuel burning ratio of ammonia.”
J-ENG’s first ammonia-fuelled engine will be a 50-bore UEC50LSJA, completed in 2025.
The development work is proceeding in a consortium programme subsidised by Japan’s national research and development agency NEDO, through its Green Innovation fund.
Hard work ahead
These and others issues will be tackled by engine designers in the months ahead. While reflecting on the successful ammonia combustion tests for his company’s two-stroke engine, MAN ES vice president and head of R&D for two-strokes, Brian Østergaard Sørensen, was pragmatic. “This is groundbreaking for both our company and the maritime industry as a whole. That said, we know we still have a lot of hard work ahead and, over the following months, will execute a testing programme that will study aspects such as heat-release, ignition, safety, pilot-oil energy fraction, NOx and N2O emissions. We then plan on rebuilding the test engine from one cylinder capable of running on ammonia to a full-scale test engine running on ammonia around the end of this year or early in 2024.”
“N2O generated during the ammonia combustion process has a GWP 273”
MAN ES two-stroke business head, Bjarne Foldager, said: “Interest in this breakthrough has been overwhelming. However, while we provide the decarbonising technology, the maritime industry must show the will to implement it. Now it’s up to the International Maritime Organisation to establish clear regulations that ensure that maritime actors are not penalised for choosing carbon-neutral fuels.”
Mr Foldager said MAN ES has “positive” expectations for ammonia because of forecasts for lower production costs, as compared to other e-fuels. “We foresee around 27% of fuel used on board large merchant-marine vessels to be ammonia by 2050,” he said.
The first engine to be introduced will be 60-bore because of its applicability to a wide range of vessel types, according to MAN ES promotion and customer support head, Thomas S. Hansen. “The interest in this engine is very high and we have received many queries across basically all large merchant-marine vessels,” he said, adding, “MAN Energy Solutions expects a quick uptake of ammonia-fuelled engines towards the end of the current decade.”